GEO engineers went to the remote Shetland Islands for a new automated monitoring job.
This was a great first opportunity to work on a Wind Farm project and GEO-Instruments’ most northerly UK project to date.
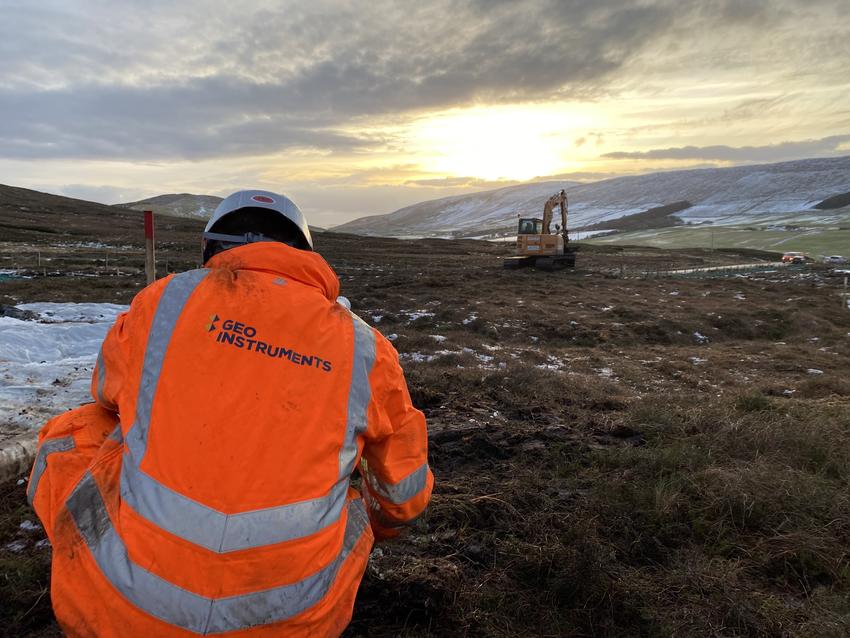
The project
Viking Energy are constructing a new Wind Farm on the central Mainland of Shetland.
Contributing towards government and global schemes to reduce CO2 emissions and increase the usage of renewable energy, the wind farm will consist of 103 wind turbines and produce enough power for 475,000 homes. Excess power not needed by local infrastructure can be supplied to the mainland via a new high-voltage cable being laid to connect Shetland to the UK power grid.
The challenge
In order to provide access to the wind farm during and after construction a new dual carriageway being constructed. Due to the ground conditions on the site it’s necessary to measure pore pressure in the peat during the construction of the road.
Mobilising engineers and equipment to site on the remote Shetland islands was a difficult task. As the installation took place in January, site conditions were also challenging. Engineers had to contend with bitter cold, heavy winds, a relatively rare instance of snowfall and short daylight hours to install the instrumentation in less than a week.
The solution
A system of 10 Vibrating Wire Piezometers and 24 settlement plates was designed for installation along the course of the dual carriageway.
The data from the piezometers is collected automatically and sent via wireless nodes to a shared gateway where it is sent and uploaded to GEO’s web-based software QuickView. The instrumentation and data collection will run autonomously for 3 years using solar power with a deep cycle back-up battery. It’s possible to remotely access the gateway to change data frequency and track battery voltages. The settlement plate measurements will be taken manually by site operatives.
Strong cooperation with the main contractor helped overcome many of the issues related to adverse weather and site-conditions. Detailed planning of logistics and works meant the instrumentation could be installed and tested within one week despite strict time constraints and the remoteness of the site.